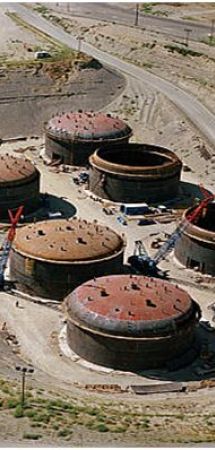
Research area
As part of an international collaboration, we are working in our laboratory to develop a model for the melting of the glass batch/feed in the melter. Using our mathematical model, we will be able to predict the glass production rate and help to optimize the entire melting process.
Nuclear Waste vitrification
In Hanford, in the northwest of the US in Washington, more than 200,000 m3 of radioactive waste is stored in underground tanks, a result of the plutonium production during the II. World war and Cold war. This waste is stored in 177 aging underground tanks, which have problems with leakage that leads to the contamination of underground and threatens the nearby Columbia River, the second largest river on the Pacific coast of North America.
In order to process and stabilize the radioactive waste, a Waste Treatment Plant (WTP) is now being built at Hanford. The radioactive waste will be mixed with glass-forming and glass-modifying chemicals and melted at 1150 °C in an electric furnace. The resulting glass will be poured into stainless-steel canisters, where the glass will cool and solidify. In the form of glass, the radioactive waste will be stable and safe for a long-term storage in an underground repository.
Although the vitrification of radioactive waste is a proven technology that has been successfully employed for decades, it has never been used on such a large scale and for such complex nuclear waste, as is stored at Hanford. The vitrification plant is thus a huge engineering challenge and one of the world's most complex remediation projects. For example, only the waste pre-treatment and separation plant (dividing the waste into low-activity and high-level fractions) has a ground plan of 165 x 65 meters, and is 12 floors high.
Our group has a long-history working on various aspects of waste glass melting at Hanford. In 2018, another two-year grant from Department of Energy (DoE USA) was awarded to our laboratory to work on the nuclear waste vitrification project at Hanford.
Selected publications
- Lee S., Hrma P., Pokorny R., Klouzek J., VanderVeer B., Rodriguez C., Chun J., Schweiger M., Kruger A. (2017). Effects of alumina sources (gibbsite, boehmite, and corundum) on melting behavior of high-level radioactive waste melter feed. MRS ADVANCES. 2, 11, 603-608.
doi: 10.1557/adv.2016.644 - Lee S., Hrma P., Pokorny R., Klouzek J., VanderVeer B.J., Dixon D.., Luksic S.A., Rodriguez C.P., Chun J., Schweiger M.J., Kruger A.A. (2017). Effect of melter feed foaming on heat flux to the cold cap. Journal of Nuclear Materials. 496, 54-65. doi: 10.1016/j.jnucmat.2017.09.016
- Lee S., Hrma P., Kloužek J., Pokorný R., Hujová M., Dixon D.R., Schweiger M.J., Kruger A.A. (2017): Balance of oxygen throughout the conversion of a high-level waste melter feed to glass. Ceramics International. 43, 13113-13118. doi: 10.1016/j.ceramint.2017.07.002
- Hujova M., Pokorny R., Klouzek J., Dixon D.R., Cutforth A., Seungmin Lee, McCarthy B.P., Michael J. Schweiger M.J., Kruger A.A., Hrma P. (2017): Determination of Heat Conductivity of Waste Glass Feed and its Applicability for Modeling the Batch-to-Glass Conversion. Journal of the American Ceramic Society. 100, 5096-5106. doi: 10.1111/jace.15052
- Lee, S., VanderVeer, B. J., Hrma, P., Hilliard, Z. J., Heilman-Moore, J. S., Bonham, C. C., Pokorny, R., Dixon, D. R., Schweiger, M. J. and Kruger, A. A. (2017). Effects of Heating Rate, Quartz Particle Size, Viscosity, and Form of Glass Additives on High-Level Waste Melter Feed Volume Expansion. Jornal of the American Ceramic Society. doi:10.1111/jace.1462
- Pokorný R., Hilliard Z., Dixon D., Schweiger M., Guillen D., Kruger A., Hrma P. (2015). One-Dimensional Cold Cap Model for Melters with Bubblers. Journal of the American Ceramic Society, 98, 3112-3118.